Unlocking the Potential of Plastic Molding Services
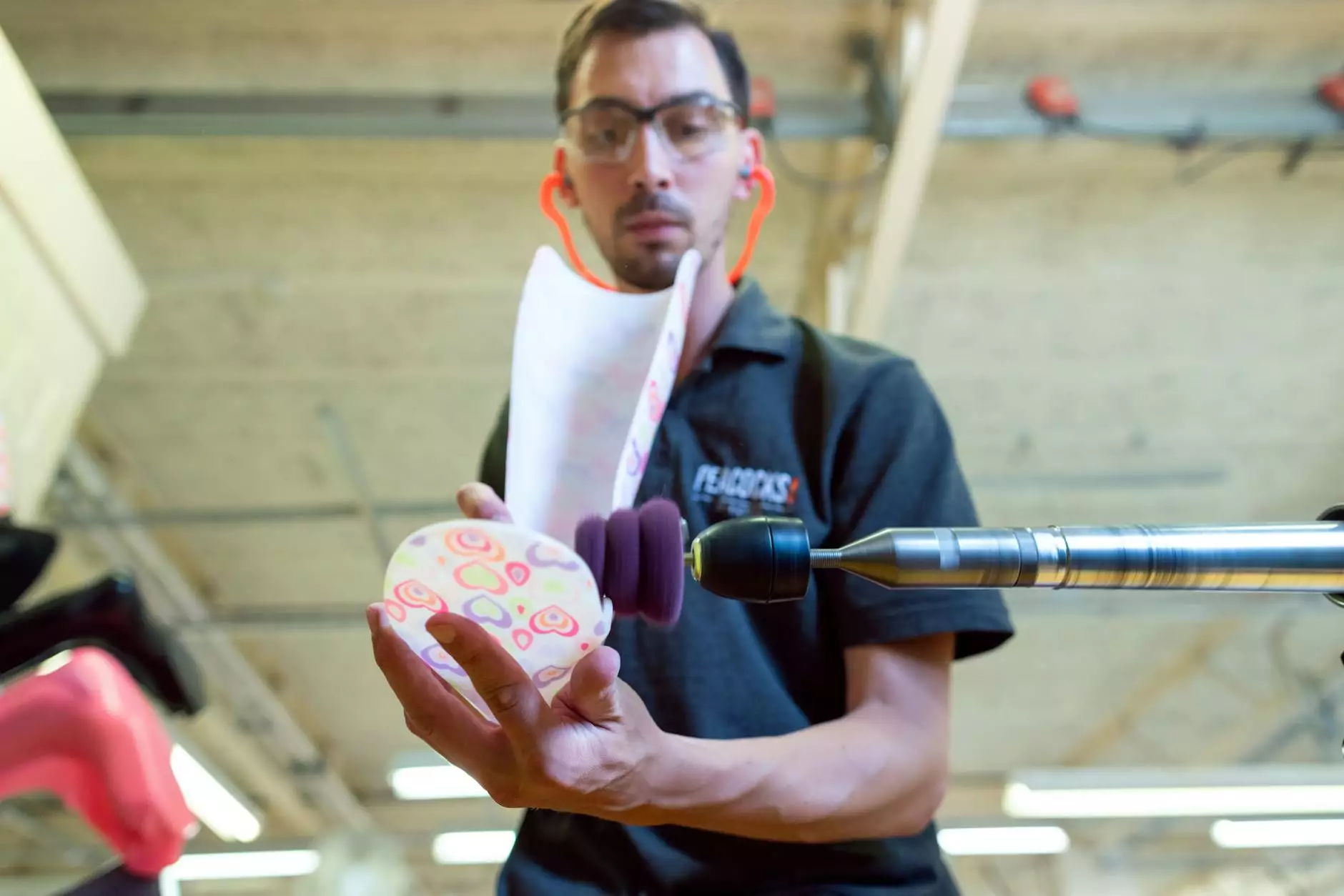
In the dynamic landscape of modern manufacturing, plastic molding services have emerged as a cornerstone of productivity and innovation. This comprehensive guide will delve into the intricacies of plastic molding, its various processes, applications, and why it is essential for businesses, especially those engaged in metal fabrication and manufacturing.
Understanding Plastic Molding: An Overview
Plastic molding is a process that involves shaping and forming plastics into specific designs using molds. This method is not only efficient but also adaptable to a wide range of products and industries. Essentially, understanding how this process works is crucial for any business looking to leverage these services.
Types of Plastic Molding Processes
There are several key processes utilized in plastic molding, each catering to different project requirements and outcomes:
- Injection Molding: This is the most common type of molding. It involves injecting molten plastic into a mold to create complex shapes with precision and consistency.
- Blow Molding: Primarily used for creating hollow plastic objects, blow molding relies on air pressure to form shapes. It’s typically used for bottles and containers.
- Extrusion Molding: This process is used to create long products such as pipes, sheets, and films. The plastic is forced through a die to achieve a continuous profile.
- Compression Molding: Often used for larger parts, this process involves placing plastic into an open mold and then applying heat and pressure to shape it.
- Rotational Molding: Utilizing a rotating mold, this method evenly distributes the plastic and is ideal for creating large items with hollow interiors.
The Benefits of Using Plastic Molding Services
Choosing plastic molding services offers numerous advantages for businesses across various sectors:
1. Cost Efficiency
Plastic molding generally reduces production costs. By producing large quantities of items in a single run, businesses can achieve economies of scale, minimizing the per-unit cost.
2. Consistency and Quality
With advanced machinery and techniques, plastic molding ensures that each product meets high standards of quality and consistency, which is vital for brand reputation and customer satisfaction.
3. Design Flexibility
The versatility of molds allows for intricate designs and shapes that may not be feasible with other manufacturing techniques. This flexibility enables companies to innovate continuously.
4. Material Variety
Plastic molding services can utilize different types of plastics, such as ABS, polyethylene, and polypropylene, giving businesses the freedom to select materials that best meet their performance and cost requirements.
5. Sustainability
Many modern plastic molding services focus on sustainability by using recycled materials and implementing energy-efficient practices, contributing to a lower environmental impact.
Key Applications of Plastic Molding
The applications of plastic molding services span across various industries, showcasing their versatility:
1. Automotive Industry
Many components in vehicles, such as dashboards and bumpers, are produced through plastic molding. This helps manufacturers reduce weight and improve fuel efficiency.
2. Consumer Goods
Everyday items, from kitchenware to toys, are made using plastic molding. This ensures durability and cost-effectiveness in mass production.
3. Medical Devices
The precision and reliability of molded plastic parts make them ideal for medical devices, ensuring safety and compliance with health standards.
4. Electronics
Plastic housings for electronic devices are often created through molding processes, providing protection and a lightweight alternative to metal.
5. Industrial Applications
Many industrial components, such as gears and connectors, are produced using plastic molding to enhance performance and reduce wear.
Selecting the Right Plastic Molding Service Provider
Choosing the right provider for plastic molding services is essential to ensure that your products meet quality standards and timelines. Here are some factors to consider:
1. Experience and Expertise
Look for a provider with a proven track record in delivering high-quality products. Experience in your specific industry can also be a significant advantage.
2. Technology and Equipment
Advanced machinery and technology can enhance the precision and quality of molded parts. Ensure your provider invests in up-to-date equipment to stay competitive.
3. Customer Service
Effective communication and support are vital for successful collaboration. A good provider should be responsive and willing to assist throughout the entire process.
4. Quality Control Processes
Ensure the provider has robust quality assurance processes in place to minimize defects and maintain product standards.
5. References and Portfolio
Ask for references and review their portfolio to gauge previous work’s quality and suitability for your needs.
The Future of Plastic Molding Services
As technology continues to advance, the future of plastic molding services looks promising. Innovations such as 3D printing are intersecting with traditional molding processes, paving the way for even greater efficiencies and capabilities. Sustainable practices are also becoming more prevalent, with an increasing focus on reducing waste and using biodegradable materials.
1. Industry 4.0 Integration
The integration of smart technologies, data analytics, and automation is transforming traditional manufacturing. Plastic molding services are adapting to these changes, enhancing production speed and accuracy.
2. Advancements in Materials
Research into new materials, including bioplastics and composites, is broadening the horizons for plastic molding applications, making them more sustainable while maintaining performance.
3. Customization Capabilities
Future molding services will likely offer even more customization options, allowing businesses to produce tailored solutions that meet exact specifications.
Conclusion
In conclusion, the significance of plastic molding services in the manufacturing sector cannot be overstated. Their benefits encompass cost-effectiveness, design flexibility, and the capability to support a wide array of industries, from automotive to medical. As businesses seek innovative ways to improve their production processes, leveraging the expertise found at companies like deepmould.net can pave the way for success. By understanding the processes, advantages, and future trends of plastic molding, organizations can position themselves for growth and sustainability in a competitive marketplace.