Silicone Injection Molding - ProMed Molded Products
Blog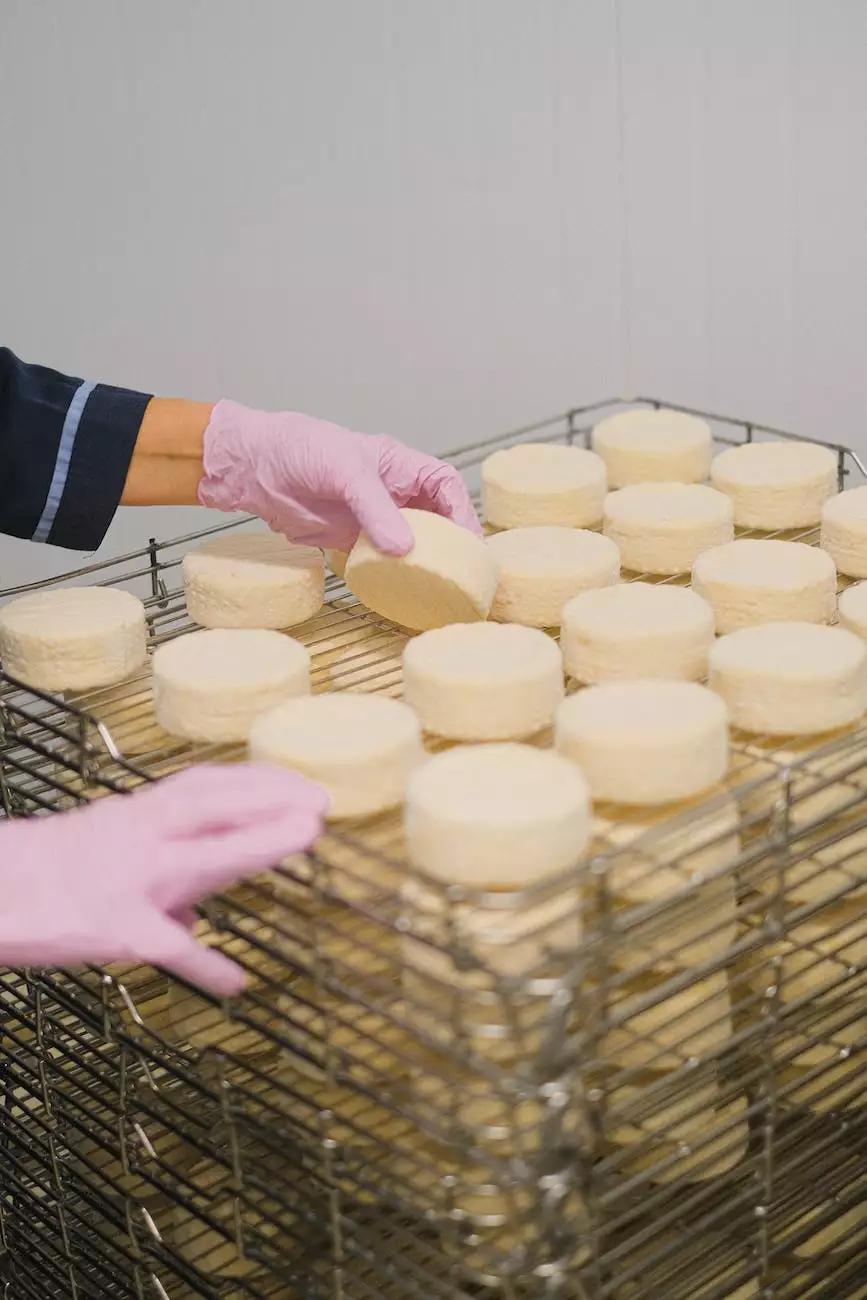
Introduction
Welcome to Phoenix Medical Services, home to ProMed Molded Products' exceptional silicone injection molding services. With our unmatched capabilities, state-of-the-art technology, and commitment to quality, we are the preferred choice for medical device manufacturers seeking reliable and precise silicone components.
Why Choose ProMed Molded Products?
At ProMed Molded Products, we set ourselves apart through our unwavering dedication to excellence. Here's why you should choose us for your silicone injection molding needs:
- Industry Expertise: With over 30 years of experience in the industry, our team possesses the knowledge and skills required to deliver top-tier silicone components.
- Advanced Technology: We leverage the latest advancements in silicone injection molding technology to ensure exceptional precision, consistency, and efficiency.
- Quality Assurance: We maintain strict quality control measures throughout the entire manufacturing process to guarantee impeccable results and adherence to industry standards.
- Comprehensive Solutions: From design assistance and prototyping, to production and validation, we offer a wide range of comprehensive solutions tailored to each client's unique requirements.
- Regulatory Compliance: We have a deep understanding of the regulatory landscape surrounding medical device manufacturing, ensuring compliance with FDA regulations and international standards.
- Customer Satisfaction: Our focus on delivering superior customer service and satisfaction is reflected in our long-standing relationships with clients.
Our Silicone Injection Molding Process
ProMed Molded Products utilizes an advanced silicone injection molding process that guarantees exceptional precision and quality. Our process includes the following steps:
- Design and Engineering: Our skilled team of designers and engineers collaborates closely with clients to bring their concepts to life, ensuring feasibility and manufacturability.
- Material Selection: We offer a wide range of medical-grade silicone materials to suit various applications, ensuring optimal performance and biocompatibility.
- Tooling and Mold Fabrication: Our state-of-the-art facility is equipped with advanced machinery for precise tooling and mold fabrication, enabling accurate reproduction of complex designs.
- Injection Molding: We employ highly automated and controlled injection molding processes to produce consistent and reliable silicone components, meeting tight tolerances and specifications.
- Post-Molding Operations: Our comprehensive post-molding operations include deflashing, trimming, cleaning, and inspection, ensuring the final product meets the highest quality standards.
- Quality Control and Testing: Rigorous quality control protocols are applied throughout production, supplemented by testing to verify the performance, durability, and biocompatibility of the finished components.
- Packaging and Delivery: We carefully package and deliver the finished silicone components, ensuring they arrive in optimal condition and on schedule.
Applications of Silicone Injection Molding
Silicone injection molding is widely used in various medical applications due to its exceptional properties and versatility. Some common applications include:
- Medical Devices: Silicone components find extensive use in medical devices such as catheters, implantable devices, surgical instruments, and respiratory devices.
- Wearable Technology: The flexibility and biocompatibility of silicone make it ideal for wearable medical devices, including smartwatches, fitness trackers, and drug delivery systems.
- Dental Applications: Silicone plays a crucial role in dental molds, orthodontic products, and oral appliances, ensuring accurate fitting and patient comfort.
- Cosmetic and Personal Care: Silicone injections are utilized in cosmetic and personal care products like silicone gel-filled breast implants, scar treatment sheets, and skincare devices.
- Drug Delivery Systems: Silicone injection molding facilitates the production of precise drug delivery systems, ensuring controlled release and patient safety.
The Benefits of Silicone Injection Molding
Silicone injection molding offers several advantages that make it a popular choice for medical device manufacturers:
- Biocompatibility: Silicone is biocompatible, minimizing the risk of adverse reactions and providing excellent patient comfort.
- Temperature Resistance: Silicone exhibits remarkable resistance to extreme temperatures, ensuring the longevity and reliability of medical devices.
- Elasticity and Flexibility: The inherent flexibility of silicone allows for easy insertion and movement in medical applications.
- Chemical Resistance: Silicone resists degradation from exposure to chemicals, making it suitable for a wide range of medical environments and sterilization methods.
- Dimensional Stability: Silicone components retain their shape and dimensions over extended periods, ensuring consistent performance and reliability.
- Electrical Insulation: Silicone possesses excellent electrical insulation properties, making it suitable for medical devices that require electrical insulation.
- Ease of Sterilization: Silicone is compatible with various sterilization methods, including autoclaving, ethylene oxide, and gamma irradiation.
Contact ProMed Molded Products - Phoenix Medical Services
For superior silicone injection molding services, ProMed Molded Products at Phoenix Medical Services is your trusted partner. Contact us today to discuss your project requirements and benefit from our industry-leading expertise.
Phoenix Medical Services 123 Main Street Your City, State, ZIP Phone: 123-456-7890 Email: [email protected]