DFM Checklist for Medical Manufacturing
Blog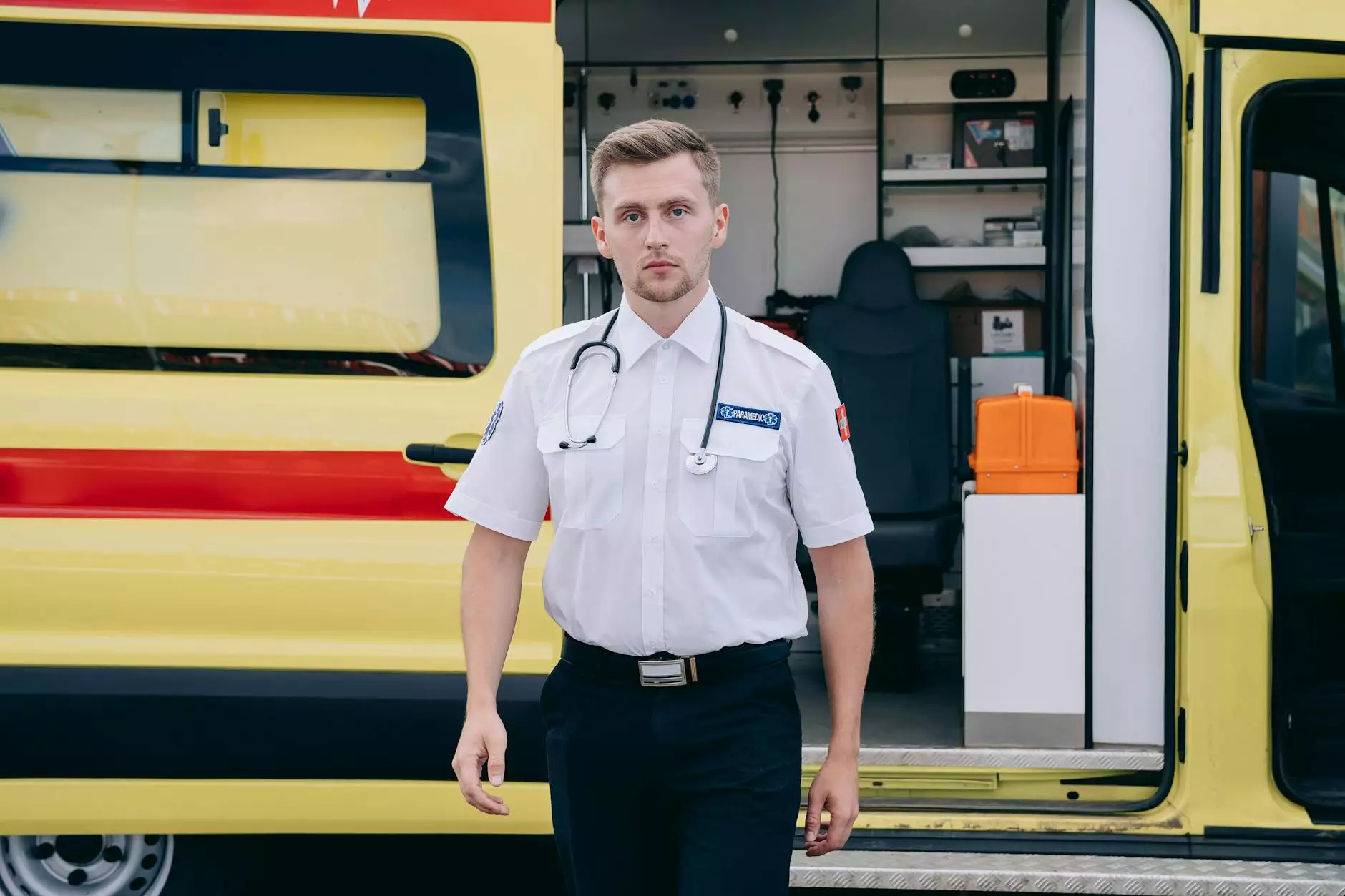
Introduction
Welcome to Phoenix Medical Services' comprehensive DFM (Design for Manufacturing) Checklist for Medical Manufacturing. In this guide, we will provide you with a detailed checklist designed to help you optimize your medical device manufacturing process and improve efficiency, quality, and overall success. Implementing proper DFM practices is crucial in the healthcare industry, where precision and reliability are of utmost importance.
Why is DFM important in Medical Manufacturing?
Design for Manufacturing (DFM) is a critical aspect of medical device production that focuses on designing products with manufacturing efficiency in mind. Effective implementation of DFM principles ensures that the design and manufacturing processes are streamlined and optimized, resulting in high-quality, cost-effective, and reliable medical devices.
DFM helps medical manufacturers address potential issues and challenges that may arise during production, such as complex assembly, material selection, and regulatory compliance. By considering manufacturing constraints from the early stages of product development, medical manufacturers can significantly reduce costs, accelerate time to market, and enhance product performance and quality.
DFM Checklist for Medical Manufacturing
1. Design for Manufacturability:
- Product Design: Ensure the design meets the functional requirements and is manufacturable at scale. Consider factors such as part complexity, tooling requirements, and assembly processes.
- Tolerance Analysis: Perform tolerance analysis to ensure proper fit and functionality of components. Optimize tolerances to avoid manufacturing defects and assembly issues.
- Material Selection: Select materials that are both suitable for the intended use of the medical device and can be efficiently and cost-effectively manufactured.
- Component Standardization: Standardize components and minimize the number of unique parts to reduce complexity and simplify manufacturing processes.
2. Assembly Process:
- Design for Assembly (DFA): Simplify assembly processes by ensuring ease of component integration, reducing the number of assembly steps, and minimizing the need for specialized tools or skills.
- Automation: Explore opportunities for automation in assembly processes to improve efficiency, reduce labor costs, and minimize human error.
- Testing and Quality Control: Integrate testing and quality control measures at various stages of the assembly process to identify and address potential issues early on, ensuring the production of reliable and high-quality medical devices.
3. Compliance and Regulatory Considerations:
- Regulatory Compliance: Ensure your medical device design and manufacturing processes comply with relevant industry regulations and standards, such as ISO 13485, FDA regulations, and EU MDR.
- Risk Management: Implement risk management practices throughout the design and manufacturing processes to minimize potential hazards and assure patient safety.
- Documentation: Maintain accurate and comprehensive documentation that records design changes, manufacturing processes, and quality control measures. This documentation is crucial for regulatory audits and product traceability.
Conclusion
In conclusion, optimizing your medical device manufacturing process through the implementation of effective DFM principles and practices is vital for success in the healthcare industry. By considering manufacturing constraints from the early stages of product design, standardizing components, streamlining assembly processes, and ensuring regulatory compliance, you can enhance efficiency, reduce costs, and deliver high-quality medical devices. Remember to continually review and update your DFM practices to adapt to new technologies, regulations, and market demands.